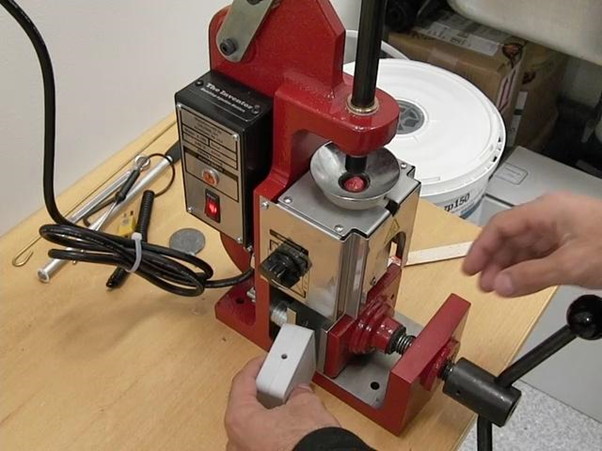
Plastic injection molding is a popular manufacturing technique used to create parts and products from thermoplastic and elastomeric materials. Unlike other methods, injection molding allows for complex shapes and detailed designs to be produced with repeatable precision.
In addition, it is a relatively fast and cost-effective process that can be used for both small and large production runs. As a result, plastic injection molding is the preferred manufacturing technique for many applications across a wide range of industries. Let’s take a closer look at what is injection molding and its applications.
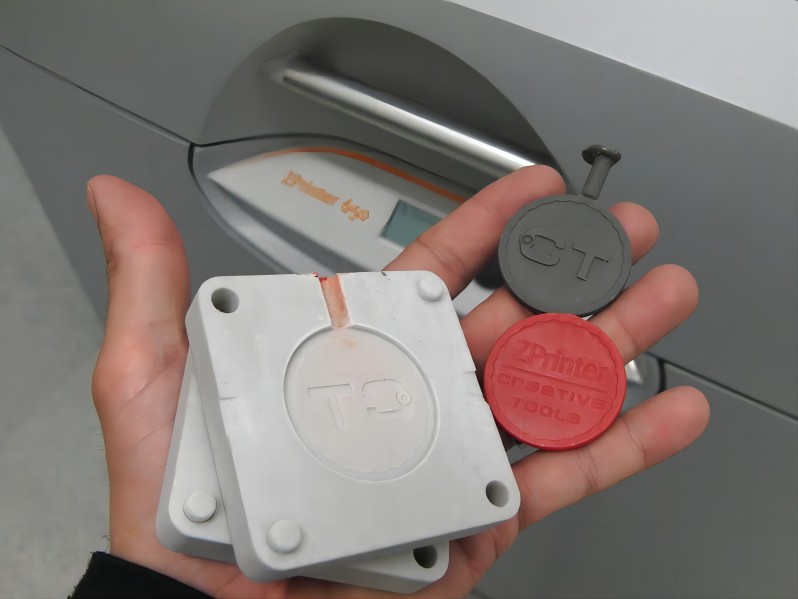
Plastic injection molding is a versatile manufacturing technique
Plastic injection molding is one of the most versatile and cost-effective methods of mass-producing a variety of plastic products. Using a heated plastic resin and a custom-created mold, designers are able to form plastic into almost any shape with precision detail. In comparison to other forms of manufacturing, the process is incredibly efficient with very little wasted material. Injection molding can also be used for quick cycle times, allowing for large numbers of identical parts to be produced in rapid succession – perfect for items like toys or bottles. What’s great about this manufacturing technique is that even complex designs can be created with relative ease.
Through the use of multiple pieces, intricate shapes and intricate patterns can easily be fabricated from basic building blocks.
Plastic injection molding has enabled manufacturers to produce an enormous variety of products on a mass scale, giving them an immense advantage in today’s global marketplace. For these reasons, it remains one of the most popular techniques used today in manufacturing all sorts of consumer goods and industrial products – making it the gold standard when it comes to modern manufacturing techniques.
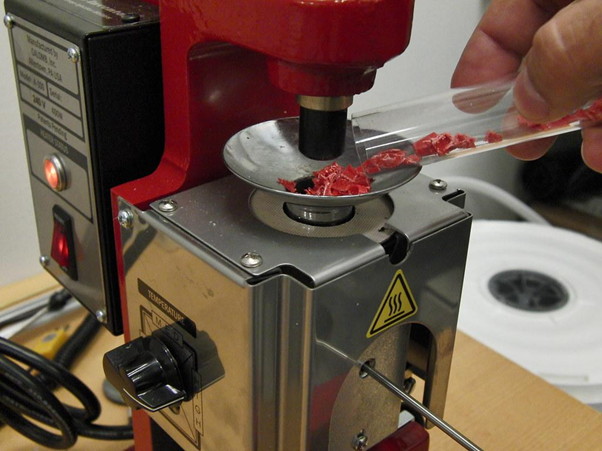
It can be used to create a variety of products, from toys to car parts
Plastic is one of the most versatile materials in the world. It is light, durable, and can be produced quickly and cost-effectively. These qualities make it an excellent material for manufacturing many different items on an industrial scale. From toys to car parts, containers to building components; plastic is used to create products in almost every corner of the industry.
What’s more, plastic comes in a wide range of compositions and colors, providing manufacturers with even more options when it comes to product design. Admittedly, the uncontrolled disposal of plastic waste has had a detrimental effect on our environment – but that doesn’t mean that this remarkably resilient material should be written off altogether. By better understanding its qualities, discovering new ways of recycling it, and investing in research and development for alternative plastics; this resource could still have an enormously positive impact on our lives for years to come.
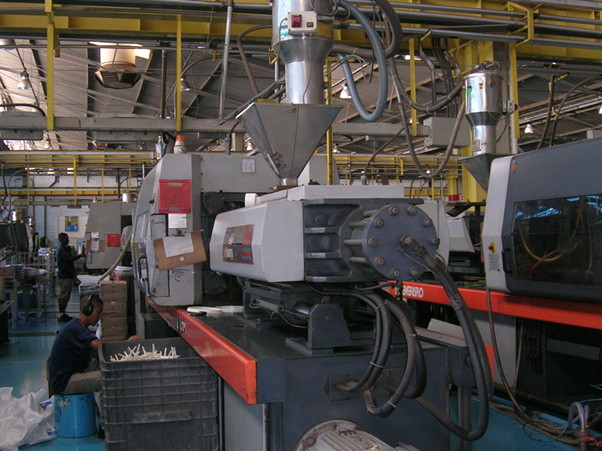
The process is relatively quick and easy, and it doesn’t require much manpower
The idea of starting a project can be daunting, particularly when it involves manual labor. For those who are short on time and resources, the thought of having to invest an abundance of effort may put them off. Fortunately, there are some tasks that don’t demand a lot of either. One example is the process of moving soil around on a construction site.
It is relatively quick and easy, meaning it doesn’t require much manpower or take up substantial time. All that is needed are sufficient tools, such as wheelbarrows and shovels.
The entire process can then be completed within hours instead of days or weeks. As such, there is no need to worry about having to employ reliable help because, without putting too much stress on wallets or schedules, the job can still effectively be done with minimal resources available. With these approaches in mind, it should be easy to begin working on projects with ease and confidence.
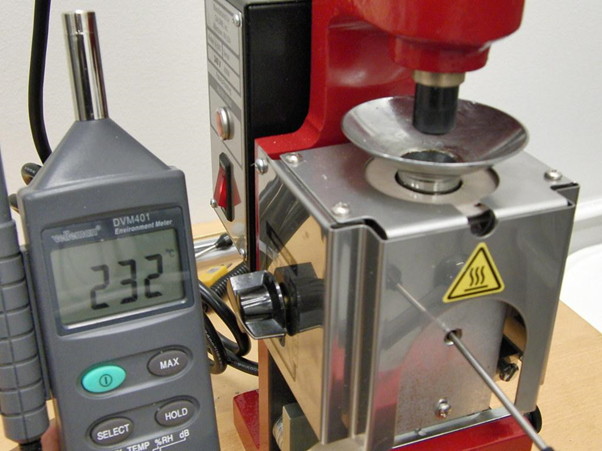
Injection-molded plastic is strong and durable, making it ideal for many applications
Injection-molded plastic has been a popular choice of material for an array of products since its invention. It is renowned for its strength, durability, and versatility; it can be manipulated into almost any shape while still maintaining its structural integrity.
Such characteristics make injection molded plastic ideal for consumer and industrial applications, from automotive designs and components to consumer electronics. In fact, many industries rely on the high-performance characteristics of injection molded plastic, such as superior anti-corrosion properties and terrific resistance to extreme temperatures or chemical exposure.
Furthermore, injection molded plastic can be formed through a variety of processes with different materials depending on the desired final product – making it incredibly adaptable. With so many benefits packed into one compound material, injection molded plastic continues to be a go-to choice for product designers and manufacturers due to its durability and reliability. Its exceptional qualities remain unparalleled even after years of technological advancements – ensuring that injection-molded plastic will only become more popular over time.
The technique is also relatively economical, which makes it a popular choice among manufacturers
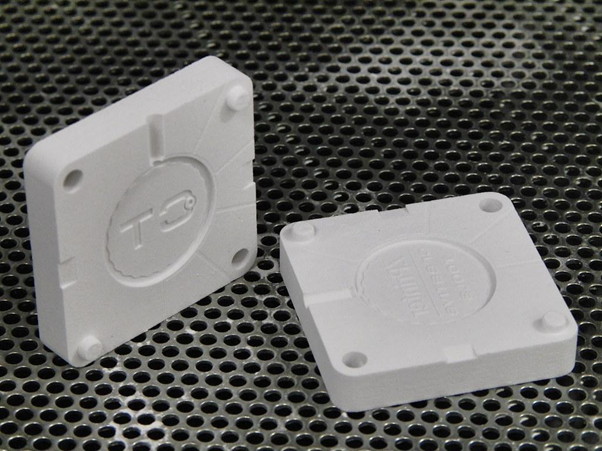
Economical manufacturing techniques are incredibly desirable in today’s market, so it is not surprising to see the popularity of a certain production process known as “economical manufacturing” increase in recent years.
Despite its name, this technique is actually far more than just economical; it is also incredibly efficient and can produce a high-quality product in a very short time. With traditional methods of production, manufacturers have to worry about waste and inefficient resources but with economical manufacturing, these kinds of problems can easily be avoided. Not only does the process significantly reduce costs due to its efficiency and speed, but it also eliminates any need for extra inventory storage or overhead fees associated with manufacturing and storage.
This makes the technique an economic option that has become highly sought after by many manufacturers as well as store owners looking for quick turnarounds on orders. The speed and cost savings of this method make it an especially attractive choice for those looking for an economical alternative to traditional production processes. With so many advantages, there is little surprise that this tool has become so popular in recent years.
Conclusion: All in all, plastic injection molding is a versatile and popular manufacturing technique that can be used to create a variety of products. The process is relatively quick and easy, and it doesn’t require much manpower. Injection-molded plastic is strong and durable, making it ideal for many applications.
The technique is also relatively economical, which makes it a popular choice among manufacturers. Have you ever used a product that was made with this manufacturing technique? If so, leave us a comment below and let us know what you think!
WellerPCB is an advanced electronics contract manufacturer in China with experienced team to provide professional support on PCB frication, PCB assembly, components sourcing, electrical testing and molding injection services.